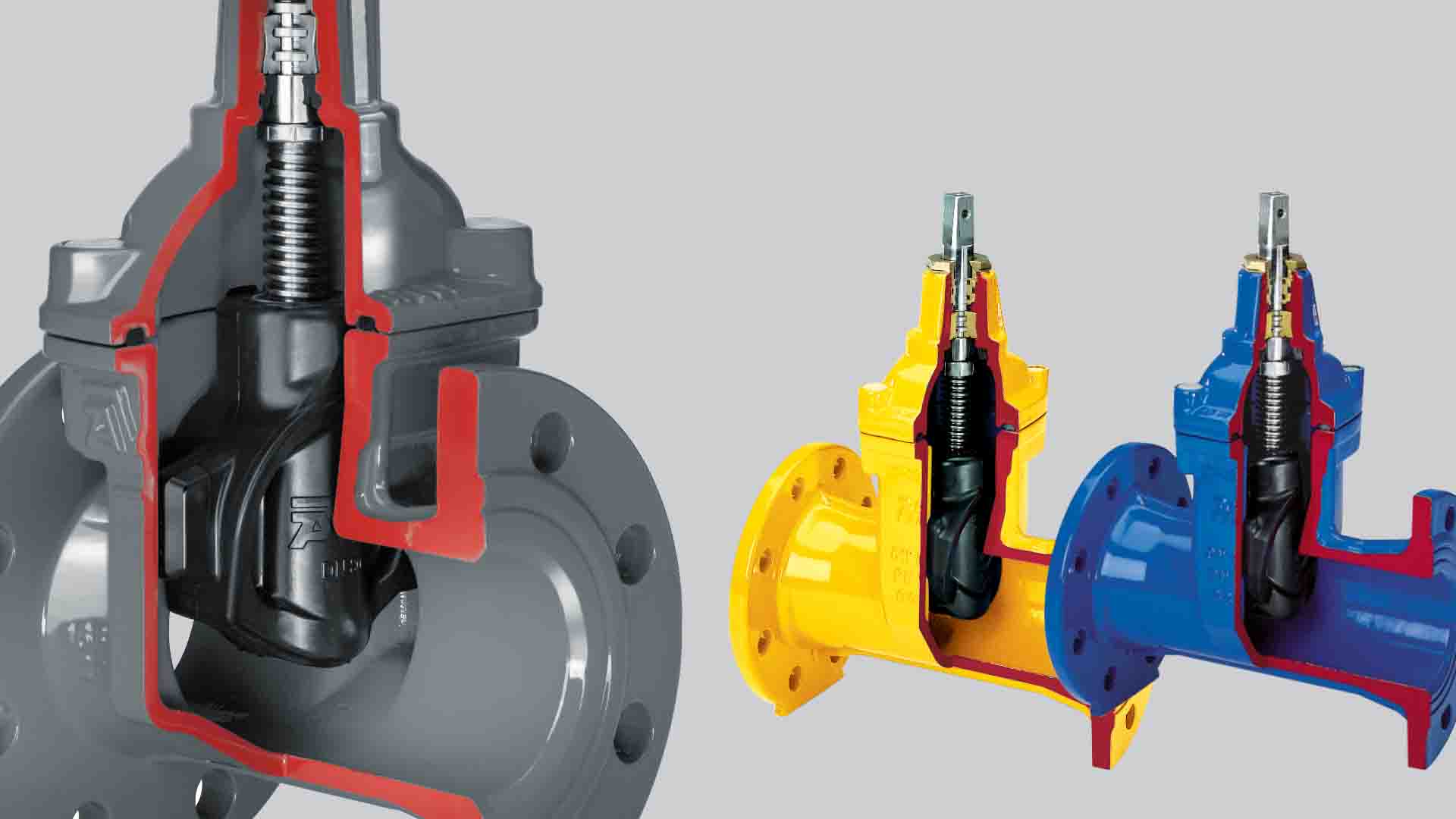
Renowned quality
AVK has been in the valve business for almost 50 years. When Niels Aage Kjaer took over his father¡¯s smithy in 1970, he developed the first gate valve, a resilient seated socket ended gate valve with a lot of new technical features. He soon realized that the quality of the internal rubber components are of paramount importance for the valve performance, so back in 1975 he decided to take full control of this and acquired a neighbouring rubber factory. Today, AVK GUMMI A/S develops and manufactures rubber compounds to AVK's and other customers' uncompromising standards of excellence.
AVK's continuous focus on high quality and innovation has paved the way for a global reach, and the gate valve range has been widened substantially to meet local requirements around the world. Today, AVK offers gate valves according to global standards and with a wealth of end connections and material configurations ¨C in total more than 100 variants to meet the requirements from AVK International¡¯s region, and more than 300 variants in total from the AVK Group of companies.
Things to consider when choosing a gate valve
Please refer to the pages what is a gate valve, unique wedge design, sturdy gate valve design, end connections and accessories to find much more details. In our Insights section you will find general technical information about our products, highly relevant for choosing the right solution; our guide how to choose the right gate valve, the article about the main European standard for gate valves and how AVK complies, an article about why third party approvals can help you make the safe choice, and details about our coating process.
Design features of AVK gate valves
Fixed, integral wedge nut prevents corrosion, made of low lead brass approved for drinking water
Wedge shoes fully vulcanised to the wedge core ensuring smooth operation and maximum corrosion protection
AVK¡¯s wedge rubber features an excellent bonding and ability to regain its shape, minimum formation of biofilm and high resistance to water treatment chemicals
Large stem hole in the wedge prevents stagnant water
Wedge stop protects seals and coating
Rolled threads increase the stem¡¯s durability
Triple safety stem sealing
Thrust collar provides fixation of the stem and low torques
The bonnet gasket is fixed in a recess in the bonnet and encircles the bonnet bolts to prevent blow-out
Countersunk bonnet bolts sealed with hot melt to protect against corrosion
Full bore ensures low head loss and enables use of pipe cleaning devices
Low operating torques ensure easy operation
Epoxy coating according to DIN 30677-2 and GSK guidelines, optionally internal enamel and external PUR coating