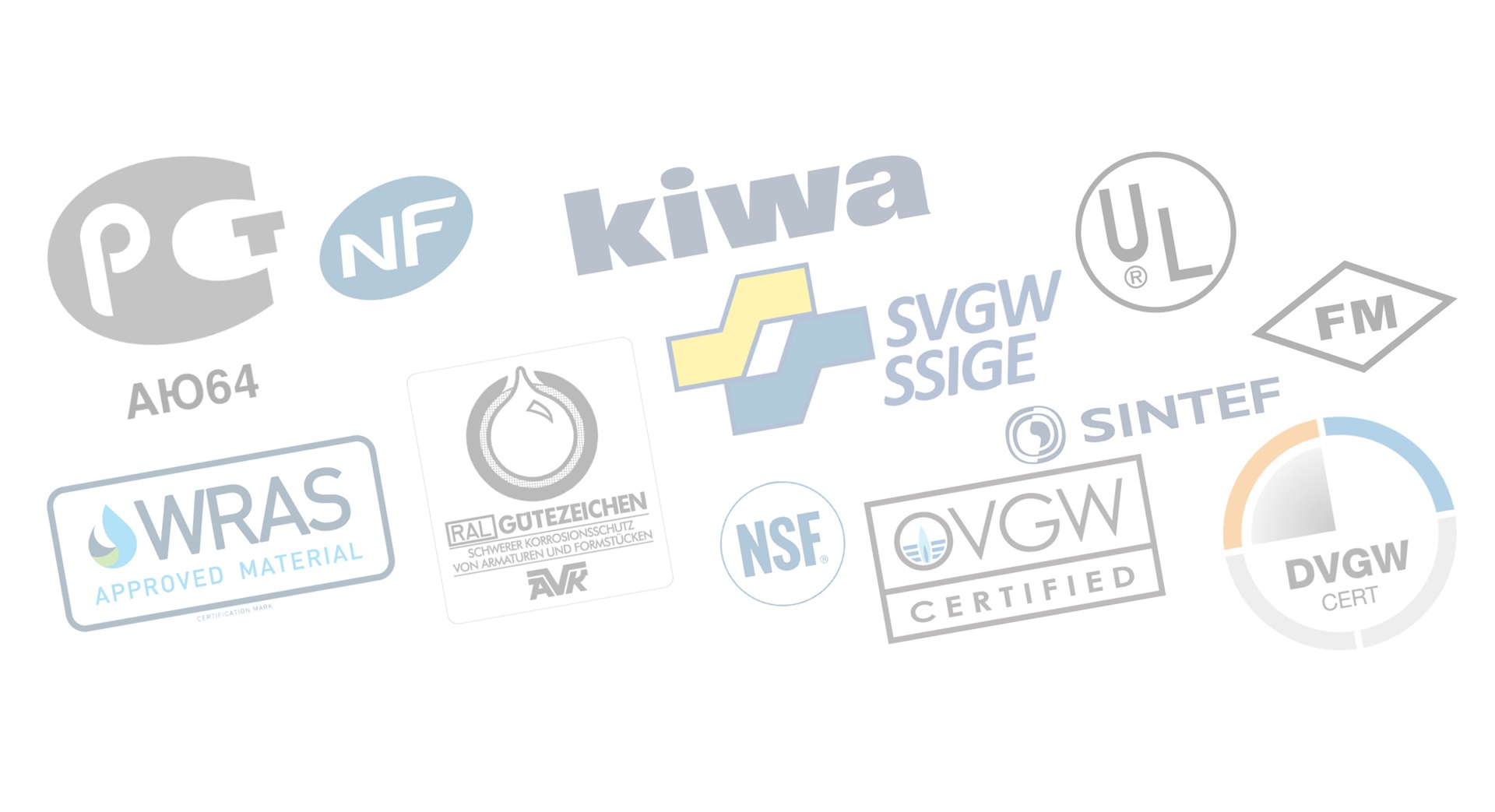
Third party approvals
For our customers, it is essential that quality and safety can be documented. This is where third party approvals come in, by establishing a range of requirements concerning valve components and finished valves.
Products are designed, tested and approved to relevant standards by AVK and its subsidiaries, and products are provided with third party test documentation. Typically this includes European standards like the EN1074, face to face standards according to EN558, flange drilling standards to EN1092-2 (ISO7005-2), hydrauling testing standards according to EN12266-1 and 12266-2, threaded designs to BS21 and BS5154 etc. Other standards are provided for other types of valves and usages as for for instance balancing and motoried control valves depending on types of valve and usage. Local standards and third party documentation is also available when relevant i.e GB-T13927-2008 and JB/T5296-1991 which are also largely built on European standards.
These approvals are especially important for drinking water applications, where it is crucial that the components do not pose a risk of contamination and do not affect taste and smell. Some of these approvals specifically deal with the materials such as rubber, epoxy coating, plastics and brass used in valves, and some with the complete valve and function. Surprisingly, there are very few pan-European standards. Instead, standards are determined at national level and even in some cases by the local water works in the respective countries.
In the driver¡¯s seat concerning rubber
Taking rubber as an example, Germany has its own set of standards for rubber compounds used in drinking water applications, and the same is valid for other European countries as well as for US, China and Australia, among others. Altogether there are at least 20 different sets of standards for rubber compounds worldwide.
Today, AVK is the only valve manufacturer with its own rubber compound manufacturing site. We have developed a family of rubber compounds for drinking water that we consider universal, as it complies with the broadest possible range of approval requirements. However, some countries like Japan and South Korea have specific requirements where special compounds are required.
Anders G. Christensen, Sales and R&D Director at AVK GUMMI A/S says: "The end users of AVK valves count on us to help them navigate this welter of standards, even though this is not an easy task. Regulatory requirements themselves can be a moving target, and the number of required approvals is increasing year after year, while many of the existing approvals are undergoing constant revisions".
AVK plays an active part, not only in meeting regulatory requirements, but also in helping to establish them. ¡°At present, we are working with the German authorities to help define and secure a transition to a new approval system that is even better than the previous one¡±, says Anders G. Christensen.
Attention on brass and epoxy
It is evident that materials like brass and epoxy coating also are of high importance, as these, if not chosen or applied correctly, may also contaminate drinking water. For instance, new EU standards for brass have resulted in a positive list of approved brass materials aiming to set limits for cadmium and lead emission that might migrate into the drinking water. Consequently, AVK has implemented a new brass material for all components, which are in contact with drinking water. Furthermore, only epoxy manufacturers with the main drinking water approvals are selected for AVK valves, and the coating process in our factories strictly follow the application recommendations set by the epoxy manufacturers. In addition, our coating process is GSK approved.