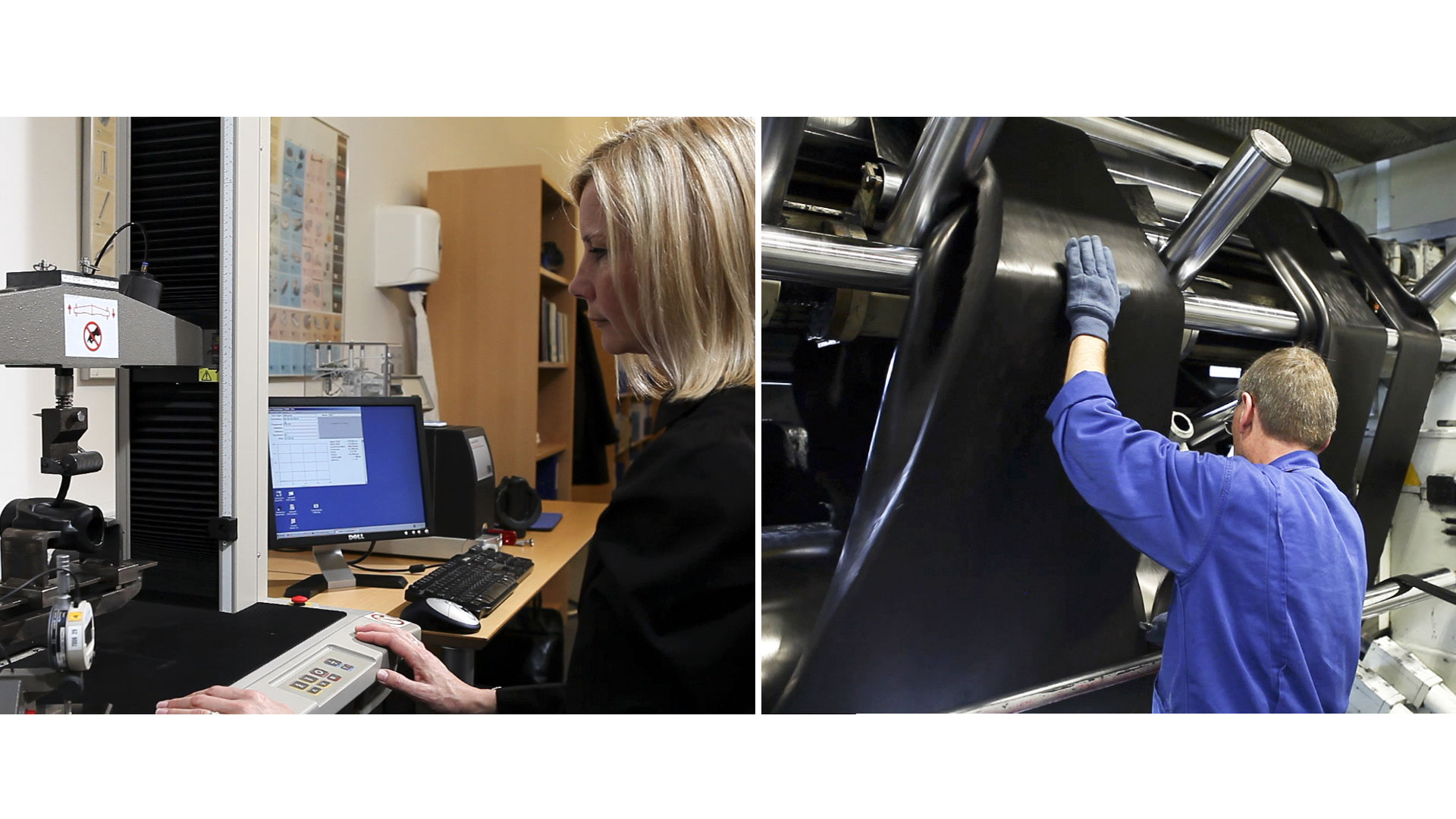
Rubber formulation
By Anders G. Christensen, AVK GUMMI A/S
Rubber compounds are far more complex than plastic and metal alloys. They are not standardised, but are subject to individual formulation. This makes it impossible for users to specify by ingredients and therefore focus should be directed towards properties and of course approvals required for the actual application.
Basically, any rubber formulation consists of polymer, filler, plasticiser and a curing system. In addition, anti-degradants, processing aids and other functional components may be applied. The polymer provides the main rubber characteristics, depending on its chemical design.
In this example, we have chosen EPDM. Three monomers can be combined in chains with varying length, side branches, ratio and sequence. All of these parameters are of decisive importance to the characteristics such as strength, permanent deformation, etc.
After having chosen the polymer, it is time to look into the fillers. The most important group is carbon black, which provides additional strength, regulates friction, flexibility, thermal and conductive properties. Depending on the structure, carbon black can alter the properties significantly.
In addition to carbon black there is a number of ¡°white fillers¡±, e.g. silica, chalk and kaolin. In general, these fillers provide less reinforcement, and most of them have an adverse effect on chemical resistance.
Now it is time to select the plasticisers. They regulate the hardness and act as homogenizers. For EPDM there is a range of plasticisers of which mineral oil is the most common.
Finally, it is time to look into the curing system. Basically, two systems are relevant for EPDM: Sulphur and peroxide. When using a sulphur system, the compound will generally be fast curing, while a peroxide system will provide low compression set, low taste and smell and much better thermal stability. On the down side, one should be aware that an additional process step is required: Post curing. This is in order to eliminate decomposition products that would otherwise cause bad smell and taste.
As mentioned, other functional ingredients might be added. Processing aids will not only provide easier demoulding and better flow properties, but will often also change the surface of the rubber part, which might be beneficial to friction, cleanability and visual appearance. However, in particular for drinking water applications, processing aids might cause micro-organisms to colonise the rubber surface and build biofilms, which again can lead to hygienic problems.
Anti-degradants are primarily used to prevent scission of the polymer backbone where this contains double bonds, as in NBR. They are generally not required for EPDM as the polymer itself is well protected. The range of anti-degradants can be split into antiozonants and antioxidants. They vary from simple waxes to very complex organic molecules.
As in any other utilisation of chemicals, one has to pay careful attention, not only to functionality, but certainly also to health and environmental impact. A large number of rubber chemicals for technical applications such as tires, hoses and belts in the automotive industry would cause a significant issue when used for food, healthcare and drinking water applications.
This is why regulators have issued positive lists, negative lists and approval programs.
At AVK GUMMI, on our own initiative, we have issued a generic certificate of conformance for all our rubber compounds, confirming that we only use raw materials which are compliant with REACH and RoHS and which do not contain animal derivatives, ozone depleting substances, conflict materials, hazardous Bisphenols or phthalates, and that our products are manufactured in compliance with EN 1935/2004, which includes Good Manufacturing Practice (GMP) and full traceability.